clean room testing
Neudorfer Engineers, an Integra Company (NEI), specializes in the testing and certification of any size or classification of Cleanrooms. Our field engineers and trained technicians perform Cleanroom certification procedures in accordance with the latest IEST-recommended practices, International Organization for Standardization (ISO) standards, owner specifications, and our company’s Standard Operating Procedures (SOP).
As a certified member of the National Environmental Balance Bureau (NEBB) and a member of the Institute of Environmental Science and Technology (
Depending upon the use of the cleanroom, the testing and certification are usually performed at initial installation and at specified intervals, whether semi-annually or annually. In each cleanroom, the concentration of airborne particles is controlled to specific limits. Cleanrooms are classified by the numbers of particles per cubic meter per minute. Sizes of particles which are controlled usually range from 0.1 to 10 micrometers. Room classifications are described in ISO-14644-1; “Cleanrooms and associated controlled environments-Part I-Classification of air cleanliness“. Cleanrooms range from ISO Class I through 9 and may be unidirectional (laminar), non-unidirectional (turbulent), or mixed airflow. Clients may choose from a variety of tests, depending upon their specific needs.
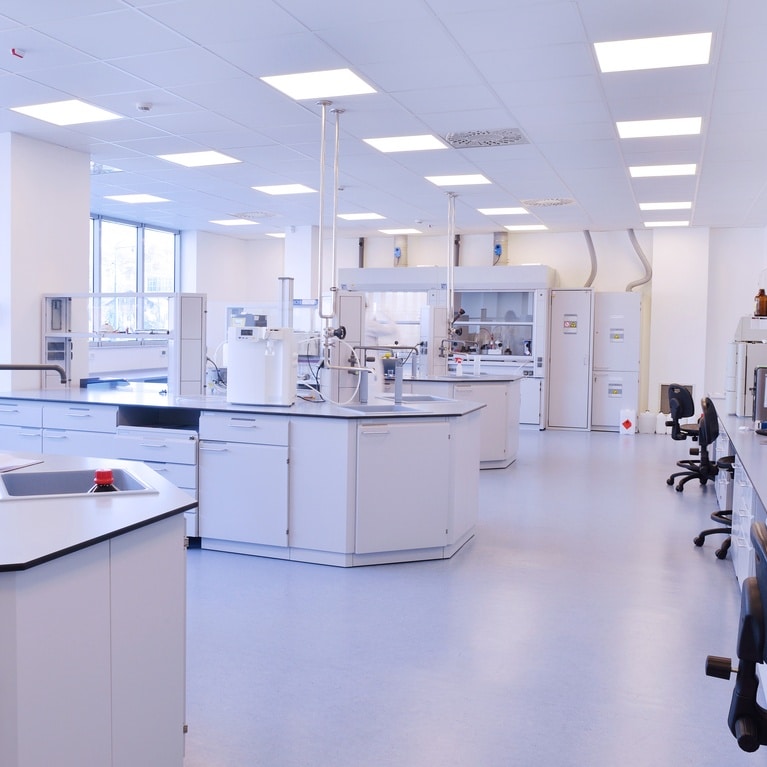
NEI provides Cleanroom testing and certification according to the ISO Standards 14644-1, 14644-2 and 14644-3-Test Methods, and IEST document IEST-RP-CC006.3 including:
- Air Flow, Volume, Velocity, Uniformity Test
- Room Pressurization
- Non-Viable Particle Count
- Temperature and Relative Humidity Test
- Room Particle Counts
NEI can also provide additional optional test services, including:
- Light Level Test
- Noise Level Test
- In-Place HEPA Filter Integrity Test
- Airflow Parallelism
- HEPA Filter Leak Testing (Bench Testing)
- Viable Particle Counting (Witness Plate)
- Visual Airflow Characterization (Smoke Test)
- Differential Pressure Gage Calibration.
- IAQ Testing and Monitoring of Industrial/Commercial Spaces
With over 39 years of cleanroom troubleshooting, benchmarking and certification experience, Neudorfer Engineers works with the design and construction teams on our clients’ behalf to bring each project to successful completion and keep your cleanrooms operating optimal levels. We provide data analysis, evaluations, and recommendations of cleanroom test results to help the project team implement corrective actions and operational procedures to achieve performance that is equal to or better than industry standards and to minimize effects on sensitive spaces, including:
- Pre-audit consulting for ISO 13485.6.4.b & c pertaining to cleanrooms & controlled environments
- Contaminant control investigations and analysis.
- Review of Personnel Protocol, Housekeeping, and Custodial Procedures.
- Review of Operational, Maintenance, Housekeeping and Custodial SOP’ manuals & Protocol documents.
- Review of Airflow Management Practices.
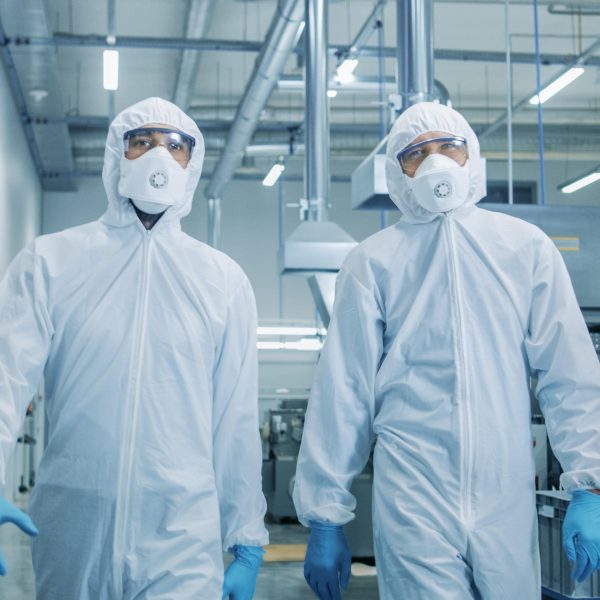
Since 1980, Neudorfer Engineers has been a leader in providing certification of contamination control services.
BSL-3 and BSL-4
Neudorfer Engineers provides evaluation and operational confirmation services for Biosafety Level 3 (BSL-3) and Biosafety Level 4(BSL-4) Laboratories.
NEI can assist in the design stage, by reviewing all drawings and specifications, to determine if the project design adheres to the specifications set forth by the industry standards for BSL-3 or BSL-4 laboratories, including the CDC-NIH Biosafety in Microbiological and Biomedical Laboratories (BMBL), or the ARS Facilities Design Standards 242.1-ARS, or additional project-specific requirements.
NEI can provide final performance verification of your BSL-3 or BSL-4 Laboratory to the applicable specifications, including:
- Equipment certification
- Facility Design and Testing
- Pressure Decay Testing
- Ventilation Design and Testing
- HVAC control Testing
- Effluent System Testing
- Appropriate Signage
- Access control
AIR MONITORING SERVICES
OSHA, NIOSH, and ACGIH have established exposure levels for various chemicals to maintain health and safety of employees. In many situations where potential exposures exist, NEI offers a variety of air comprehensive monitoring programs.
Efficiency testing is recommended by manufacturers upon installation and at regular intervals thereafter so that the emission levels are maintained within manufacturer specifications and/or permit limitations.
If Airflow Management is a concern, Neudorfer Engineers’ airflow visualization studies quantify the actual amount of airflow emitted to the adjacent environment and compare to predetermined industry standards, including:
- Fume Hood Exhaust
- Chemical Process Equipment Ventilation
- Room Pressurization
- Airflow Patterns
- Wet Bench Exhaust
- Ductwork Leak Detection
USP <797>
The U.S. Pharmacopeia’s (USP) General Chapter <797>, Pharmaceutical Compounding Sterile-Preparations has established practice standards to ensure that compounded sterile preparations (CSPs) are of high quality. These standards can help prevent harm to patients suffered as a result of contaminated preparations.
“The standards in this chapter are intended to apply to all persons who prepare CSPs and all places where CSPs are prepared (e.g., hospitals and other healthcare institutions, patient treatment clinics, pharmacies, physicians’ practice facilities, and other locations and facilities in which CSPs are prepared, stored and transported). Persons who perform sterile compounding include pharmacists, nurses, pharmacy technicians, and physicians. These terms recognize that most sterile compounding is performed by or under the supervision of pharmacists in pharmacies. This chapter applies to all healthcare personnel who prepare, store, and transport CSPs.
NEI can provide your facility with a complete package of testing services designed to meet the testing requirements of the above standard, including:
- Cleanroom Certification in compliance with current versions of IEST and CETA CAG
- Equipment Certification
- Viable Particulate Sampling
- Non-Viable Particulate Sampling
- Room Pressure Differentials
- Air Changes per Hour compliance
- HEPA Filter Leak Tests
- Ventilation Assessments
- Pressure Gauge Supply, Installation, and Calibration
- Temperature Mapping of Refrigerators and Drug Storage
BIOSAFETY CABINETS
There are three main classes of Biological Safety Cabinets (BSCs):
- Class I BSC provides personnel and environmental protection. Class I BSCs typically have an opening in the front, below a work sash. Room air is drawn past the operator, past the product, and is exhausted through a HEPA filter to a dedicated exhaust duct.
- Class II BSC (also known as Vertical Flow) provides personnel, environmental, and product protection. Class II BSCs are the most common type of BSC, with an opening in the front for operators to reach in and work with the product. Unlike a Class I BSC, HEPA filtered air is supplied to the work area inside the hood, allowing the BSC to provide product protection as well. Not only is the worker protected from the product, the product is protected from the worker. There are four types of Class II BSCs, differentiated by whether or not the exhaust air is vented to the room or ducted outside the building, and by how much air is recirculated within the BSC.
- Class III BSC provides the highest level of
personel protection. Class III BSCs are totally enclosed units. Access to the product is afforded only by gloves attached to the BSC via glove-ports.
NSF/ANSI supports an international consensus standard (Standard 49) addressing Class II BSC design, construction, and performance, which recommends certification at least annually. Individual clients may have additional industry or regulatory certification requirements, depending on BSC application.
When a cabinet is newly installed, relocated, or after panels were removed during maintenance procedures, NSF/ANSI Standard 49 requires 5 containment tests for field certifications:
- Down-flow velocity profile test
- In-flow velocity test
- Airflow smoke patterns
- HEPA filter leak test
- Cabinet leak test
NSF/ANSI Standard 49 requires 5 worker comfort and safety tests for field certifications:
- Electrical leakage
- Ground circuit resistance and polarity test
- Lighting intensity test
- Vibration test
- Noise level test
In addition, NSF/ANSI now requires a site installation assessment test for ducted units to verify that the duct system is being operated under negative pressure and that the alarm system is operating properly.
With proper maintenance and service, BSCs can provide protection for many years. Neudorfer Engineers is uniquely qualified to execute a performance evaluation of your hood for certification, troubleshooting, repairs, or general evaluation. With over 48 years of experience, NEI is a trustworthy source for testing and maintaining your biosafety cabinets for peace of mind and a cost-effective solution to unanticipated maintenance requirements
FUME HOODS
Chemical fume hoods are used to contain and exhaust chemical vapors. They come in a variety of types and designs and are used for many different operations. When using a fume hood, it is important to have proper airflow, in order to avoid release of chemical vapors from the face of the hood into the worker’s breathing zone. NEI offers face velocity measurement and smoke containment visualization as a means of documenting a fume hood’s performance and for comparison to current AIHA, ANSI, and SEFA standards. NEI’s testing and certification procedure is the first step within laboratory chemical safety management programs. NEI delivers assistance with preventative maintenance and inspections, chemical exposure monitoring, and periodic ASHRAE 110 testing to provide clients with complete programs for fume hood management
ANSI/ASHRAE 110, ANSI Z9.5-2003, and SEFA 1-2002 testing procedures verify the performance of laboratory fume hoods, including:
- Face Velocity Grid Test
- Flow Visualization or Smoke Test
- Tracer Gas Containment Test (ANSI/ASHRAE 110 only)
ASHRAE (American Society of Heating, Refrigerating and Air-Conditioning Engineers) has defined the following 3 modes for evaluating fume hoods.
- As Manufactured (AM): The AM mode requires the manufacturer to test the fume hood in their facility. Manufacturers provide the test data with the hood.
- As Installed (AI): The AI mode is performed after the unit is installed and prior to use by laboratory personnel. The AI mode is the most common mode used.
- As Used (AU): The AU mode is a dynamic test performed in an actively occupied lab. This test is usually used as a diagnostic test to ascertain the nature or source of a problem.
UNIDIRECTIONAL (LAMINAR) FLOW UNITS
Laminar Flow refers to flow of air in a single direction (unidirectional) with very low turbulence. In a horizontal Clean Bench, air flows straight out of the hood towards the operator. In a true Vertical Flow Clean Bench, the air flows directly down onto the work surface, then out into the room.
(
IEST-RP-CC-002 recommends the following certification tests:
- Air Flow Velocity;
- HEPA/ULPA Filter Installation Leak Test
- Induction Leak Test / Back-Streaming Test, as applicable
- Lighting Level, as applicable
- Noise Level, as applicable
- Vibration, as applicable